An esteemed hosiery manufacturer, renowned for producing high-quality socks for local and international markets, recently revolutionized its drying operations with our advanced radio frequency (RF) technology.
RF Systems’ state-of-the-art RF dryer has transformed the company’s production process, solving inefficiencies and achieving remarkable results in terms of quality, savings and sustainability.
The hosiery industry is characterised by the demand for high-quality production with minimal defects, fast turnaround times and energy-efficient operations. A common challenge for manufacturers is to achieve even drying of delicate fabrics without compromising their quality or elasticity, all while keeping energy costs and production downtime under control.
Prior to implementing RF technology, the Italian hosiery company was relying on outdated drying processes that required a lot of manpower, energy and inconstancy. These methods resulted in prolonged drying times, increased operating costs, and variability in product quality, problems that hindered the ability to scale up operations efficiently.
RF Systems’ radio frequency dryer uses electromagnetic waves (Radio Frequency Technology) to provide fast and even drying, ensuring uniform results on all fabric types. The technology is designed to preserve the natural elasticity and appearance of delicate materials, while significantly reducing energy consumption and production time.
The RF dryer was seamlessly integrated into the company’s production line. The technology was adapted to the specific needs of the manufacturer, offering flexibility for drying various types of hosiery and allowing the team to fine-tune the process according to production requirements.
Benefits and results
- Improved efficiency: drying times have been reduced the convejor dry speed at 6.5 mt/min, enabling faster production cycles.
- Energy savings: the innovative design of the RF dryer dramatically reduced energy consumption compared to traditional methods.
- Improved quality: uniform drying eliminated shrinkage and maintained the natural elasticity of hosiery.
- Reduced labor requirements: a process that previously required multiple operators has been simplified and reduced to one.
- Sustainability: the elimination of water and inefficient heating methods contributed to a cleaner, more environmentally friendly operation.
The company achieved a significant return on investment: savings from reduced energy consumption and increased efficiency covered the cost of the RF dryer within a year. In addition, the ability to deliver consistent, high-quality products in a shorter timeframe improved their reputation in the market.
A company representative declared:
“Our only regret is that we did not adopt this revolutionary technology sooner! It has revolutionized our operations, exceeded all expectations and set a new standard for our industry. We were so impressed with the results that we have already purchased a second machine to further expand our capacity.”
The integration of RF technology proved to be a transformative solution. By solving critical inefficiencies and delivering unprecedented results, RF Systems has demonstrated the immense value of innovation in modern sock manufacturing.
Are you ready to revolutionize your manufacturing process? Contact RF Systems today to find out how our cutting-edge technology can improve efficiency, reduce costs and elevate your operations to new levels.
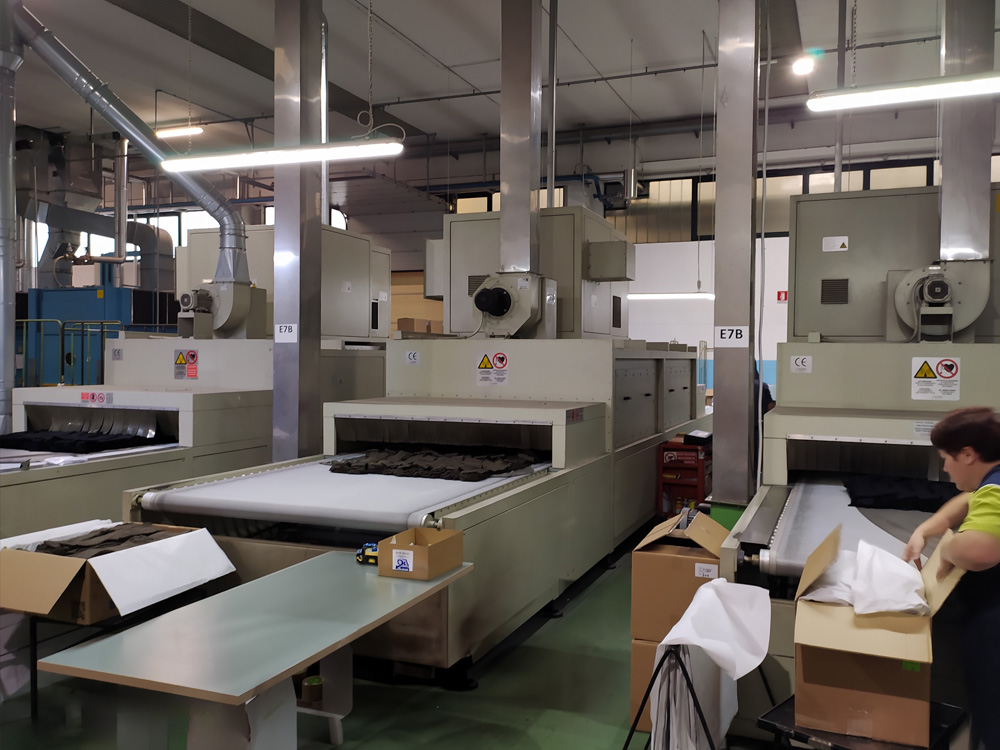
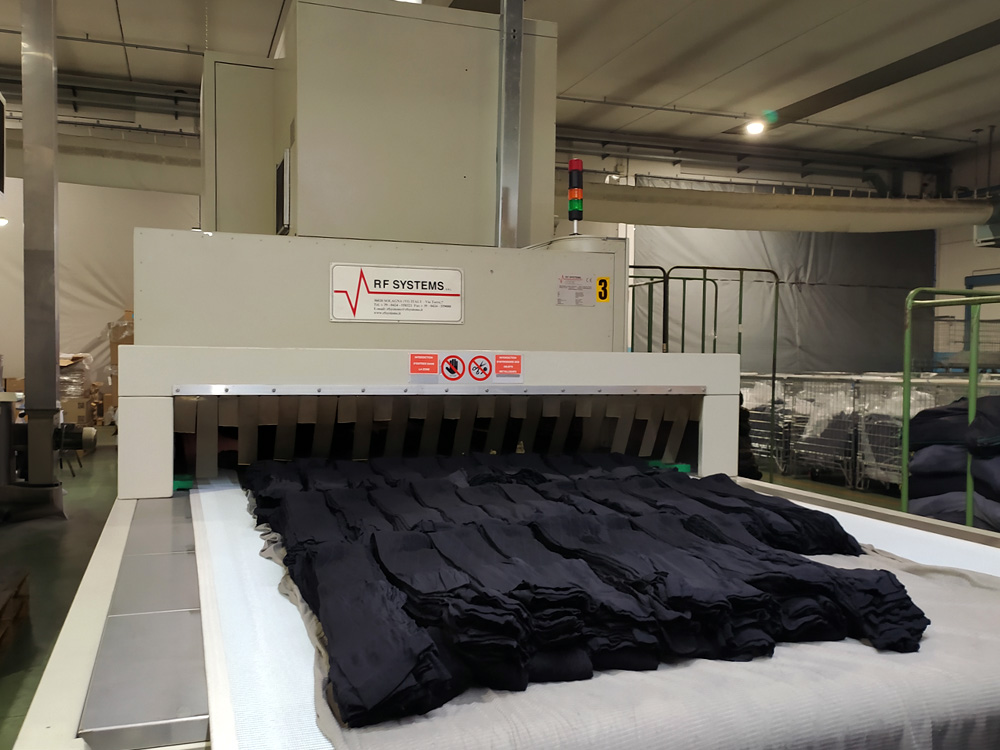